Ok, starting over, yesterday I began this blog and something went wrong I lost the last half of my text and all my photos . . . . . . .
Greetings again from Kauai. Today we did manage to see and sit in the sun for about 2 hours, now that’s progress.
Wow, two blogs in two days (or three now) I often don’t do two in a year!
Killing time during another rain storm and waiting for spuds to cook on the BBQ.
Todays topic has been rattling around in my head for more than a year. Some time ago I decided I wanted to be able to mount finished or partially finished items on a horizontal speed controlled turntable. This I felt would allow me to add color in a more controlled manner than when I do this on the lathe with the wood vertical. I wanted a device that would spin horizontally, be easy to adjust it’s spin speed, be reversible, be cheap and dependable. This is a photo of my first attempt. I’m utilizing a small chuck I use on my mini because it is easy to get threads to match from readily available bolts and threaded rod not like the M33 on my oneway.
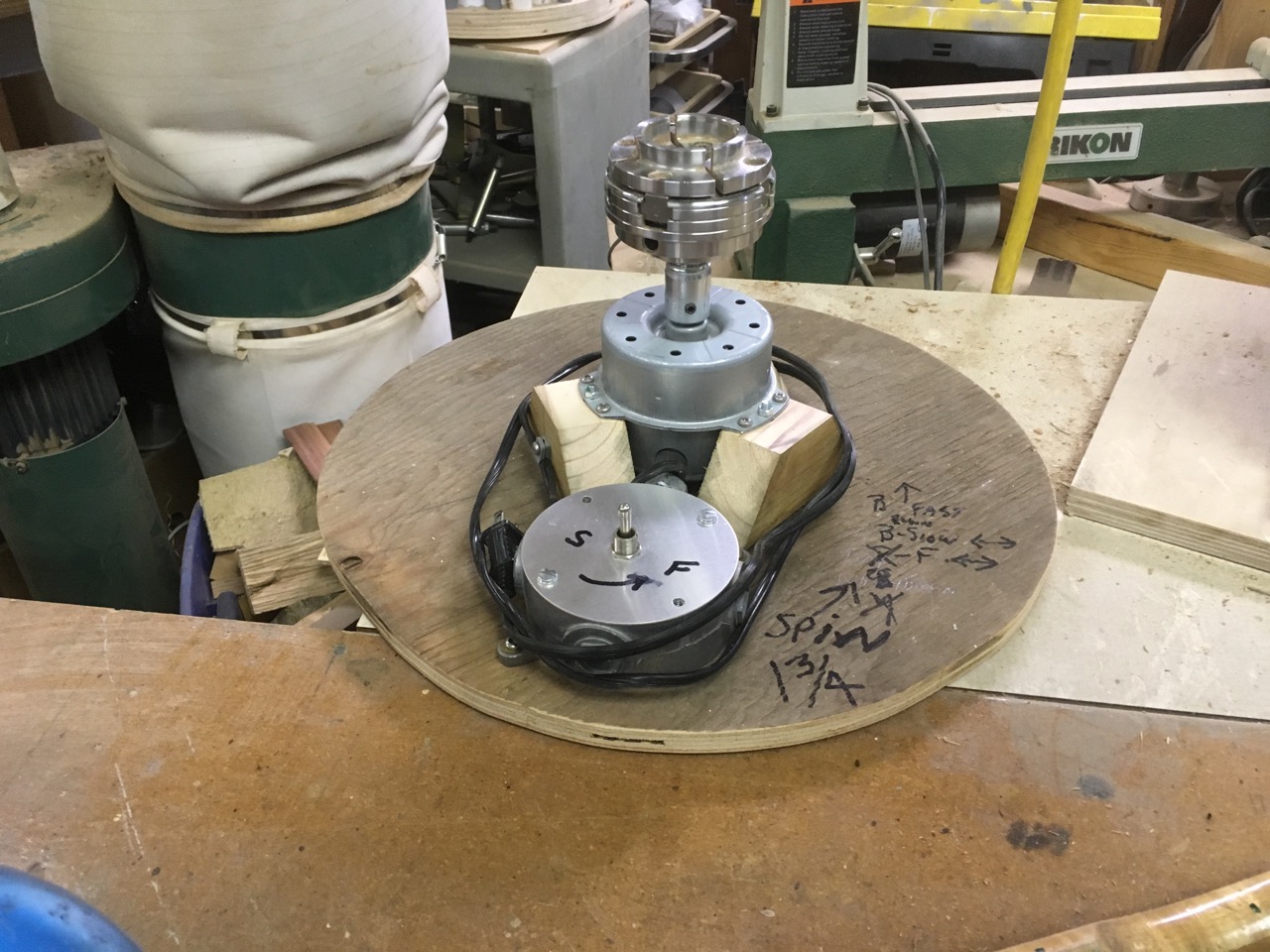
I started out thinking that I could use a fan motor and have collected a number of them over time but it soon became apparent that they were not as powerful or controllable as I wanted, primarily because they are not ‘brush’ type motors. I then switched my focus to an overhead fan. Knowing that people remove and replace them occasionally I advertised locally for a free used one but had no luck. There were a few that came available for a small cash outlay but being the cheap guy I am I stuck to my guns and decided not to pay for something I wasn’t certain would work for me.
In the end this all worked out for the best. I am known to peruse and buy on line from several local auctions and wound up with a “tool lot” that had an old beat up cord shredded 1/2″ drill. Ok, this should work fine, it was cheap, easy to control speed (brush type motor), reversible and top speed was about 1000 rpm.
I changed my mind about mounting the a lathe chuck directly on a motor as I did with the fan motors and instead decided to use an old Pillow block I had laying around. I took a section of 1″ 8 TPI threaded rod and turned it to fit thought the bearings of the pillow block on my small metal lathe. I turned a short section on one end to 1/2″ so it would be easily gripped by the drill. I then mounted it to a section of plywood and discovered that with a small piece of rubber under the drill it lined up perfectly with the 1/2″ end of the shaft. As can be seen below this tool will now function as a lathe as well should I want to spin wood while finishing it or ????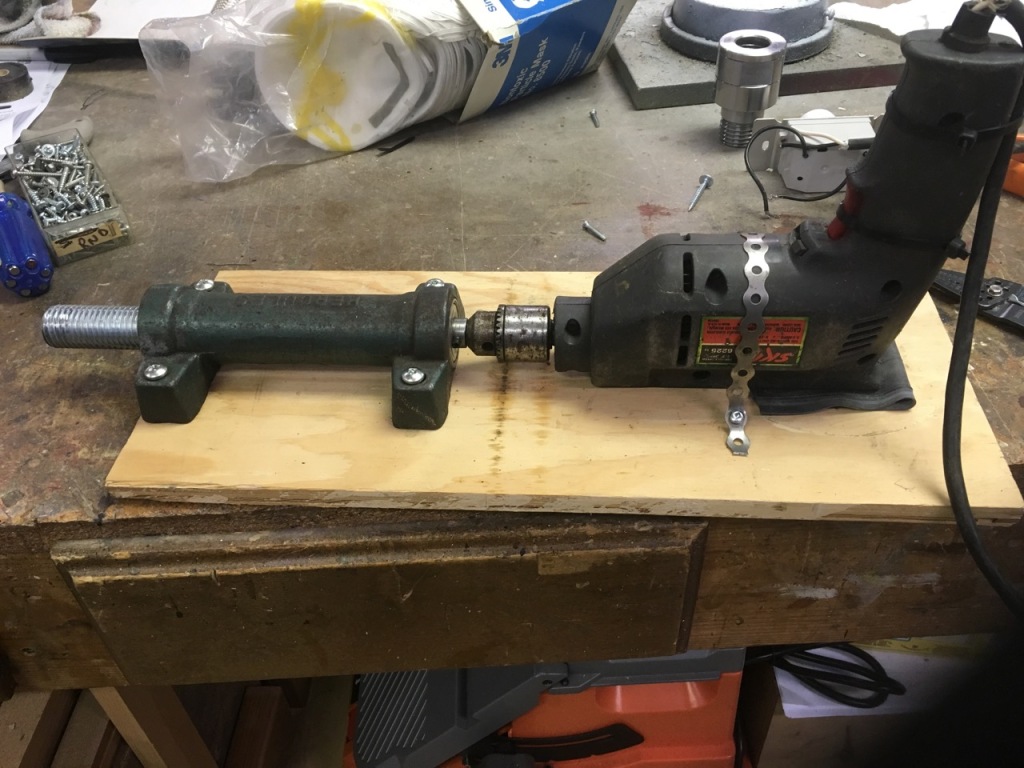
By mounting it on the edge of my heavy bench I thought it just might be able to take the shake it might get if the turned piece wasn’t quite balanced. Much to my surprise it spins with hardly a shake.

For now I am just clamping it to the work bench but soon will add some sort of fastening system. As you can see from the photo I utilized a dimmer switch in the supply line to the drill but soon discovered that I needed to be able to control the speed from above the table.
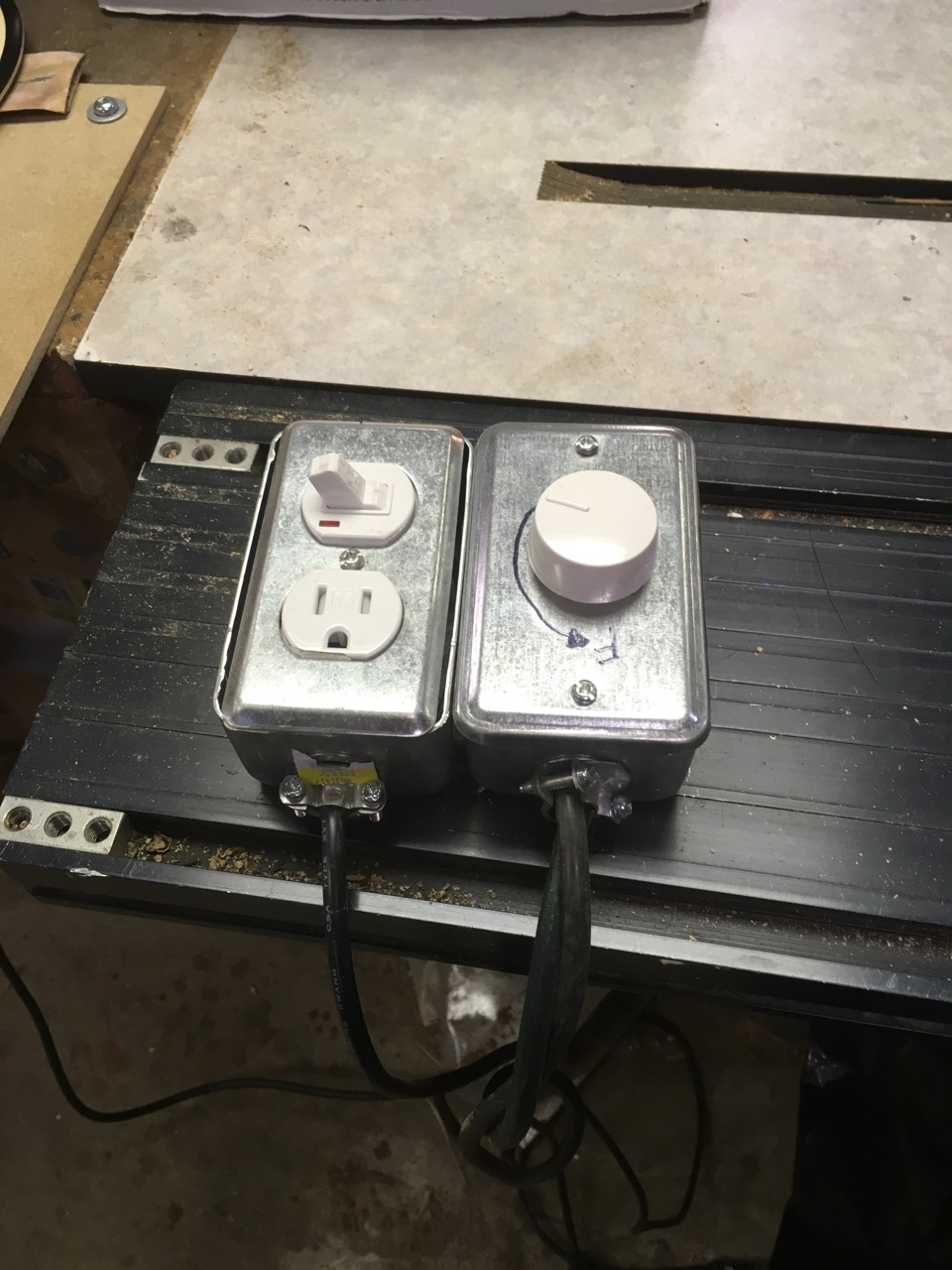
I now have a plug, on/off switch and the dimmer on long leads, these boxes are held together with a couple of magnets which allows me to separate them for storage.
Ok all works great but the dimmer I have, has the off position next to high speed and so I added an on off switch to the plug in box. The only really remaining issue is that I may want to move the reversing switch from the drill handle to the top with the rest of the controls. For now I simply use a small clamp to hold the drill switch in the full on position, and when I want to change the direction of rotation I have to remove the clamp, slide the reversing switch on the drill to the other position and re-clamp the drill switch. When I need to reverse the direction it is never in a situation where it has to happen quickly so this set up may continue to work.
Here’s a shot of my first piece with just a piece of cardboard as a table, I have since added a piece of MDF that screws to my bench top giving me a much more stable work space.

To control the paint/dye splatter I simply cut a couple of slots in a scrap piece of wood and bend a section of plastic laminate into the slots. Easily taken apart for storage. The photo below shows my first try at this when I was working with the fan motor above the bench top. I now have done away with the legs which are redundant.
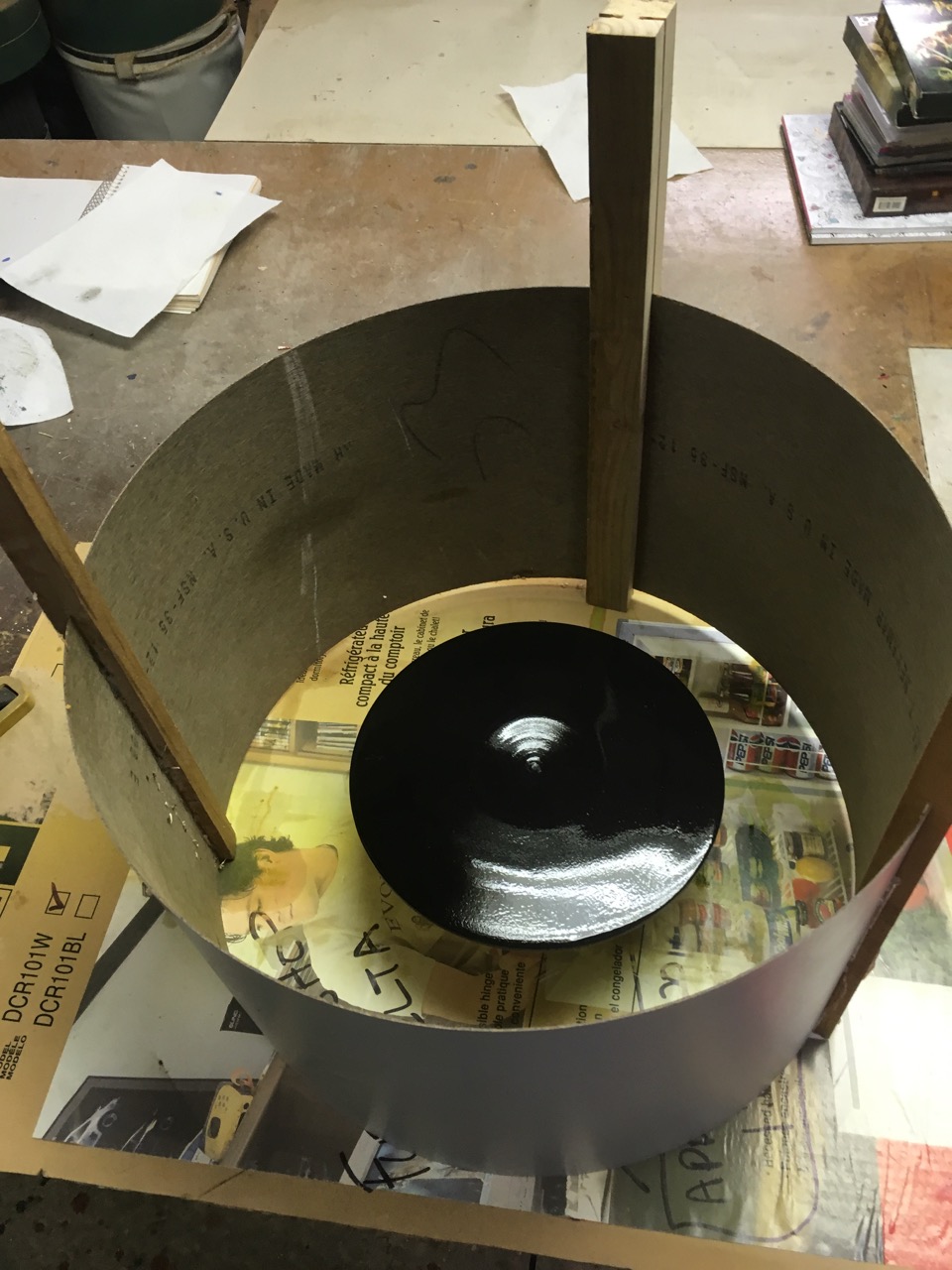
Here are a few of my first attempts. I don’t consider anything I do a failure just an opportunity to learn. The photo of the unpainted/dyed silver maple was just that. It was easy to remove the unsightly dye and start over.

I am most interested in the ability to have the paint/dye move from the center or other locations in curved line.